TURNAROUNDS
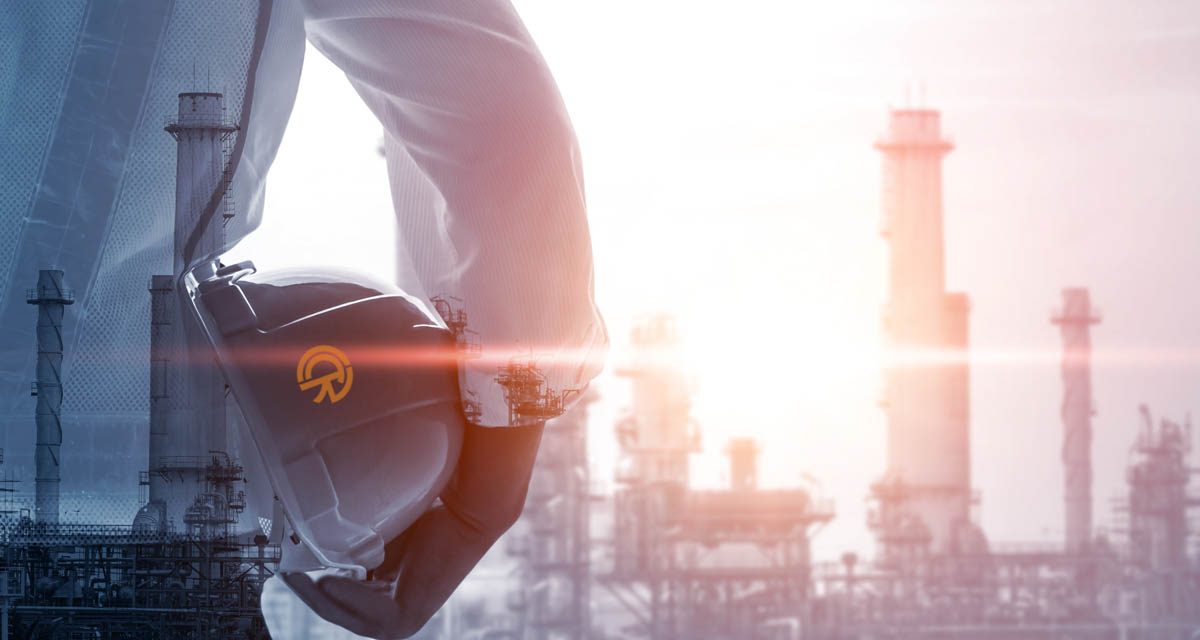
OUR WORKS IN PLANTS
Our company boasts long-standing experience in extraordinary maintenance work (Turnaround), during general plant shutdowns lasting about a month, carried out in major oil and petrochemical plants both in Italy and abroad.
OUR ACTIVITY
Scheduling, management and performances of mechanical and electro-instrumental works in Refineries, Petrochemical Plants, Power Plants.
100 YEARS ON THE DOMESTIC AND INTERNATIONAL MARKET
EXPERIENCE GOALS
OUR EXPERIENCE
- Over 250 General Turnarounds
- More than 4.8 million man-hours performed
OUR GOALS
- Safety: “no accident” during work performance through continuous and daily monitoring of compliance with laws, site specific regulations and company procedures.
- Customer Satisfation for performance quality, price competitiveness, work optimization within the set contractual time.
- Execution of the work within the contractually set time.
OUR STRENGTH
OUR STRENGTH
- Safety Culture
- Quality Culture
- Staff training and professional development at all levels
- Highly trained staff
- Equipment specific to the type of work, designed by our technicians and built in our factories
- Qualified technicians to supervise and control work performed by other contractors and/or subcontractors
- Association of Company with other Local and/or International Specialist Company
________________________________________________________________________________________________________________________________________________________________________
PRE-BID ACTIVITIES
DOCUMENT ANALYSIS
- Received documents analysis
Plant type information - Refinery layout survey
- List of work to carry out and plant and equipment isolation diagrams
- Equipment layout survey (height, accessibility, particular types of material , etc.).
- Materials technical drawings equipment, type, by plan position, installation height.
SURVEY CHECK CONFIRMATION
- Site condition assessment
- Utilities availability
- Logistics situation
- Accessibility to facilities
Materials availability
Control of possible interference with work performed by other companies
Identification of work to be performed by subcontractors
- Scaffolding
- High pressure washing
- Chemical washing
- Special lifting
- Insulations
SITE ORGANIZATION PLANNING
- Number of area coordinators
- Number of foremen ( 1/ 10 workers)
- Work equipment
- Workforce
Work schedule based on
- Client-defined turnaround timeframe
- Technical information
- Particular works required by the client
Risk analysis
________________________________________________________________________________________________________________________________________________________________________
MAIN ACTIVITIES CARRIED OUT AFTER ORDER ACQUISITION
ACTIVITY SCHEDULING
- Detailed scheduling of all planned work primavera software or order required by the client
- Workforce definition
- Organization chart processing
- Defining logistics (office containers, showers, locker rooms, etc.).
- Definition of vehicles and equipment
- Quality plan development
- Development of special safety procedures, risk analysis and safety operation plan (pos) elaboration
- Qualification of specific if required
- Processing documents for authorization procedures if required
- Preparation of structural verifications checks if any for work on pressure equipment.
________________________________________________________________________________________________________________________________________________________________________
TYPICAL ORGANIZATION CHART
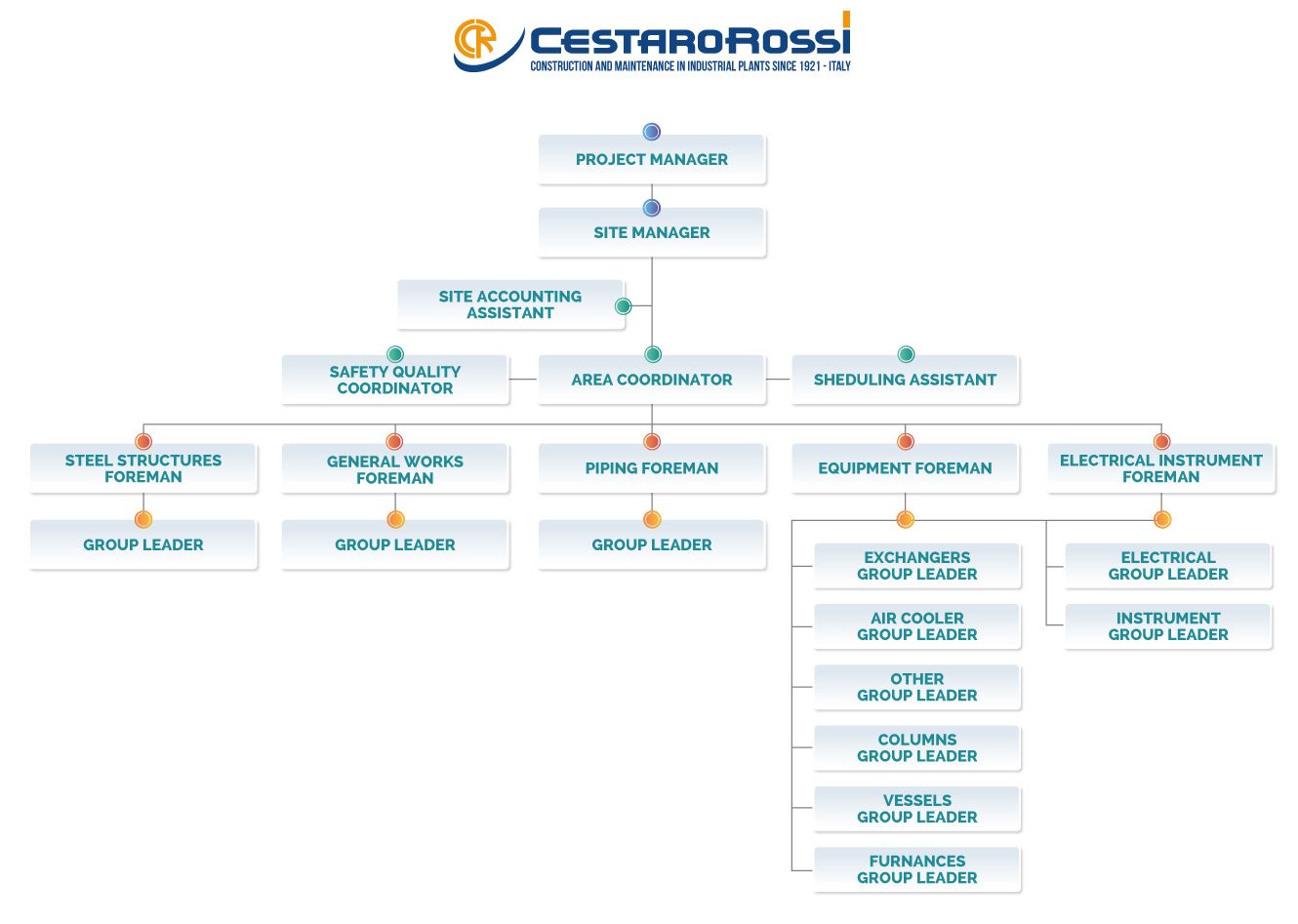
________________________________________________________________________________________________________________________________________________________________________
PRELIMINARY ACTIVITIES
SITE MOBILIZATION
- Office Containers
- Showers and toilets
- Locker rooms and canteen
DOCUMENT PREPARATION
- Preparation of documents for work authorizationMeetings with client’s technicians for
- Aspects/definition of work to be performed
- Safety for the performance of the activity
Assembly of metal structures of scaffolds where possible
Bolts and flange couplings lubrication
Training session for all personnel on the specific hazards of the work facilities
Preparation of all documentation for each foreman’s work related to the work
TRANSFER TO PLANT AREAS
- Gaskets, blind flanges, blind, test rings
- Bolts
- Toolboxes with equipment (tirfort, slings, wrenches, hydraulic screwdrivers, etc.)
- Dedicated equipment (motorized tube bundle extractors, bundle conveyor machines)
- Crane
- Fork lift
- Compressors and electric generators
- Electro and moto welders
________________________________________________________________________________________________________________________________________________________________________
SHUTDOWN ACTIVITIES
ACTIVITIES CARRIED OUT DURING THE PLANT SHUTDOWN
- Support activities to the client’s operating units for remediation and isolation of plant and equipment
- Piping prefabrication and assembly
- Fittings and valves maintenance
- Equipment maintenance (heat exchangers, air coolers, pressure vessels, columns, etc.).
- High pressure water equipment washing
- Tube bundles replacement
- Tube bundle retubing
- Furnaces maintenance and restoration
- Steam generators maintenance and restoration
- Equipment internal components and replacement (column plates)
- Welded shim restorations
- Partial restoration of equipment and components partial replacement
- Valve maintenance
- Overhaul and maintenance of electronic and pneumatic instrumentation in the control room and onsite
- Laying/replacing electrical cables
- Overhaul and maintenance of mt and bt electrical panels
- Maintenance of distribution and control equipment in electrical substations
- Electricity distribution network maintenance
- Maintenance and overhaul of electric power transformers
- Safety valves maintenance/revision/ calibration and testing
- Support activities to the client’s operating units for circuit restoration and plant commissioning
________________________________________________________________________________________________________________________________________________________________________
MANAGEMENT ACTIVITIES
MANAGEMENT ACTIVITIES CARRIED OUT DURING PERFORMANCE
- Daily meeting of work done and scheduling of work to be done the next day
- Monitoring and verifying the application of all quality, safety and environmental procedures, both corporate and site-specific.
- Daily meeting for security issues
- Daily meeting for coordination of work
- Daily audits in the field, for all activities carried out, to verify compliance with safety regulations and constant application of the provisions of the Operational Safety Plan drawn up
- Work program update and countermeasures to be taken where and if necessary
- Organization of unforeseen work
- Processing and providing all necessary documentation to external and internal auditing bodies
- Control and verification of work performed by subcontractors
- Waste Management
- Issuance of work acceptance certificates
________________________________________________________________________________________________________________________________________________________________________
REDUCTION OF TIME AND COSTS
MEASURES TO REDUCE
COSTS AND OPERATION TIMES
- Before the turnaround start
- Start erection of scaffolds metal structures at least 30 days before start-up.
- At least 15 days before start-up Supervisors and Coordinators are present onsite to analyse activities to carry out organization of work and documentation
- During turnaround
-
- Use of two washing areas where possible
- Equipment washing during 2nd and 3rd shifts
- Bolting and filling equipment with water for testing during 2nd and 3rd shifts
- Multispecialist personnel: welders/tubers, switchers/columnists, carpenters/tubers, electricians/instrument makers.
-
________________________________________________________________________________________________________________________________________________________________________